NewsDetails
Revealing the Production Processes of Seamless Steel Pipes: The Differences Between Hot Rolling and Cold Rolling Technologies and Key Points for Quality Control
author:Zhantong time:2025-06-12 18:13:00 Click:111
In the industrial manufacturing sector, seamless steel pipes, with their structural advantage of being free from welds, have become a critical foundational material in industries such as energy transportation and machinery manufacturing. The performance of these pipes fundamentally hinges on their production processes. Currently, hot rolling and cold rolling are the mainstream manufacturing processes for seamless steel pipes, yielding pipes with significant differences in precision, strength, and application scenarios due to their distinct technological characteristics. This article delves into the principles, procedures, and core aspects of quality control for both processes, providing professional references for practitioners and procurement personnel.
I. Introduction: Process Determines Performance, Technology Influences Application
The production process of seamless steel pipes directly determines their core performance attributes such as strength, precision, and surface quality, thereby influencing their suitability for different applications. Hot rolling and cold rolling, as the two major mainstream processes, have distinct focuses: the former emphasizes efficient production of large-diameter, thick-walled pipes, while the latter targets high-precision, thin-walled products. Understanding the technological differences and key points of quality control between the two is crucial for ensuring pipe performance and optimizing production and procurement decisions.
II. In-Depth Analysis of Hot Rolling Process
(1) Process Principles and Core Advantages
The hot rolling process involves heating round steel billets to a high-temperature plastic state and using rolling mills to extrude and elongate them into hollow steel pipes. The core advantages of this process lie in its high production efficiency and low cost, making it particularly suitable for the large-scale manufacture of large-diameter, thick-walled pipes, widely applied in fields such as building structures and oil and gas transportation pipelines.
(2) Detailed Production Process
Billet Preparation: Select standard-compliant round steel billets and strictly control their chemical composition and physical properties. Heat the billets to an appropriate temperature in a heating furnace to lay the foundation for subsequent plastic deformation.
Piercing Process: Use a piercing mill to pierce the heated billets, transforming solid billets into hollow shells. This is a critical step determining the inner diameter of the steel pipes.
Rolling and Sizing: Further adjust the wall thickness and length of the shells through elongation rolling, followed by precise calibration of the pipe diameter using a sizing mill to ensure dimensional compliance with design requirements.
Cooling and Finishing: Cool the steel pipes rapidly using air or water cooling methods, followed by straightening, pipe cutting, and other finishing processes to enhance surface smoothness and dimensional accuracy.
(3) Key Equipment and Technical Parameters
The core equipment for the hot rolling process includes piercing mills, rolling mills, and sizing mills, whose performance directly impacts production efficiency and product quality. During production, it is essential to strictly control parameters such as heating temperature, rolling speed, and reduction to prevent defects such as cracks and uneven wall thickness during high-temperature deformation.
III. In-Depth Analysis of Cold Rolling Process
(1) Process Principles and Core Advantages
The cold rolling process involves processing shells at room temperature through multiple passes of cold drawing or cold rolling dies to achieve high-precision forming of steel pipes. Compared to hot rolling, cold-rolled steel pipes offer advantages such as high dimensional accuracy, excellent surface finish, and thinner wall thickness, making them commonly used in manufacturing mechanical components and tubes for precision instruments.
(2) Detailed Production Process
Shell Pretreatment: Conduct surface treatments such as pickling and lubrication on the shells to remove oxide scale and reduce the friction coefficient, creating conditions for cold working.
Cold Drawing/Cold Rolling Process: Use cold drawing machines or cold rolling mills to apply tensile or compressive forces to the shells, gradually deforming them in dies to achieve target dimensions and performance requirements.
Annealing and Finishing: Cold working can lead to metal hardening, necessitating intermediate annealing to restore material plasticity. The final finishing process further calibrates dimensions, polishes surfaces, and enhances product quality.
(3) Key Equipment and Technical Parameters
The cold rolling process relies on equipment such as cold drawing machines, cold rolling mills, and annealing furnaces, with die precision directly determining the dimensional tolerance of the steel pipes. During production, it is crucial to strictly control parameters such as drawing force, die clearance, and annealing temperature to prevent issues such as uneven deformation and surface scratches.
IV. Hot Rolling vs. Cold Rolling: Technological Differences and Application Comparisons
(1) Performance Differences
Hot-rolled steel pipes, due to high-temperature processing, exhibit higher surface roughness and relatively lower dimensional accuracy but possess uniform internal microstructure and stable strength performance. Cold-rolled steel pipes, on the other hand, are renowned for their high precision and excellent surface quality but may experience localized stress concentration due to work hardening, necessitating improvement through annealing treatments.
(2) Cost Comparisons
Hot rolling requires significant equipment investment but offers high production efficiency and relatively low energy consumption, making it suitable for large-scale production. Cold rolling involves complex processes, high equipment maintenance, and processing costs, particularly significant in the manufacture of thin-walled, high-precision products.
(3) Application Scenarios
Hot-rolled steel pipes are commonly used in fields with lower precision requirements, such as building structures, oil and gas transportation, and general machinery manufacturing. Cold-rolled steel pipes, with their high precision and superior surface quality, are widely applied in precision manufacturing industries such as hydraulic systems, automotive components, and medical devices.
V. Key Points for Quality Control
(1) Raw Material Quality Control
Conduct rigorous chemical composition analysis and flaw detection on round steel billets to ensure they are free from internal cracks, inclusions, and other defects. Simultaneously, inspect surface quality to prevent billet flaws from leading to product scrap.
(2) Production Process Monitoring
Continuously monitor key process parameters such as hot rolling temperature and cold rolling drawing force to ensure stable production processes. Regularly maintain equipment and calibrate die precision to prevent product quality issues due to equipment wear.
(3) Finished Product Quality Inspection
Test the mechanical properties of steel pipes through methods such as tensile testing and hardness testing. Measure pipe diameter and wall thickness using calipers and thickness gauges, and employ flaw detection equipment to inspect surface and internal defects, ensuring products meet standard requirements.
VI. Conclusion
Hot rolling and cold rolling processes each possess unique advantages, collectively supporting the application of seamless steel pipes in multiple fields. Mastering the technological differences and key points of quality control between the two not only helps enterprises optimize production processes and enhance product competitiveness but also provides a scientific basis for procurement decisions. With technological innovations in the industry, such as the emergence of continuous rolling and high-precision cold rolling processes, seamless steel pipe production will advance towards higher efficiency and precision. If you have questions about process practices or selection, feel free to leave comments for discussion.
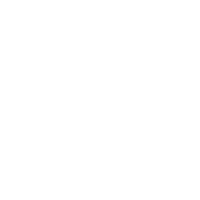
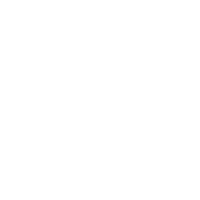
—— Contact:Manager
—— Tel:+86 15231788966
—— Email:info@zhantongpipe.com
—— Url:https://www.zhantongpipe.com
—— Address:Mengcun Hui Autonomous County, Cangzhou City, Hebei Province